Ultra Low Level Phosphorus Removal in Utah
December 2021
SUMMARY
Jordanelle Special Service District (JSSD) water treatment facility treats water from multiple communities in the area south of Park City, Utah.
With approximately 375,000 gallons per day (gpd) average flow, this municipal wastewater MBR (membrane bioreactor) facility discharges to the Timpanogos Canal and Wasatch Canal and eventually to the Jordanelle Reservoir. With a future effluent total phosphorus (TP) limit of 0.06 mg/L (90-Day Average), this facility was given one of the lowest TP limits in Utah. They had been trying to achieve this low TP limit using aluminum sulfate (alum) for phosphate removal. The facility also used sodium hydroxide (caustic) to supplement the water alkalinity to offset the acidic aluminum sulfate. However, even with high alum doses, it proved difficult and occasionally insufficient for maintaining such a low P concentration in their effluent. Then, in November of 2021, the Jordanelle facility trialed an alternative chemical for P removal, using Neo Water Treatment’s Neo WaterFX 300. WaterFX 300 was able to keep this facility TP compliant year-round, while simultaneously reducing the need for alkalinity supplementation with caustic. The reduction in chemicals required to remove phosphorus at this facility proved to be an operational and financial benefit.
Background
Designed and constructed by Bowen & Collins in conjunction with Suez, the facility was completed in 2008 with Zeeweed 500D membranes and an initial design capacity of 1.2 MGD. The plant was left idle until 2020 due to the financial crisis and abrupt crash of the housing market. The plant has an A2O configuration for biological nutrient removal, and solids are dewatered via belt filter press.
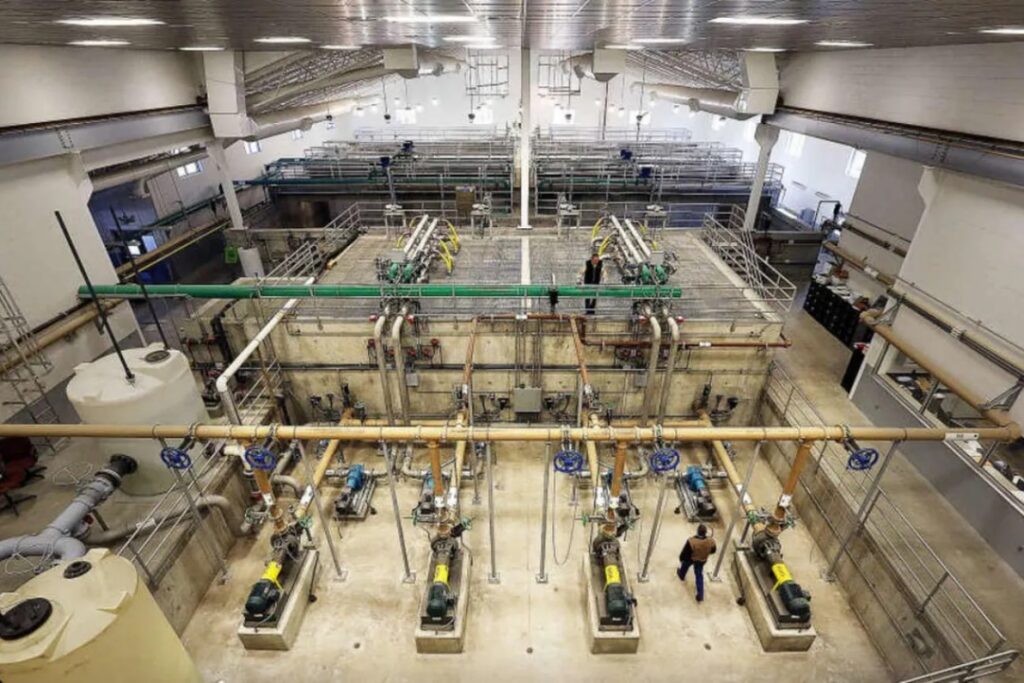
Figure 1: Inside the Jordanelle MBR Facility
Before the introduction of WaterFX 300 in 2021, the plant operation included dosing approximately 120 (gpd) aluminum sulfate into the aerobic basin. As shown in figures 2 and 3, this dose of alum consistently struggled to maintain the effluent within compliance of its TP discharge permit limit of 0.06 mg/L. With the high dosage of alum, the plant needed to supplement the alkalinity in the aeration basin. They used 50% caustic at a dose of up to 50 gpd to provide alkalinity for the biological nitrogen removal process, and to maintain the alkalinity and pH within the limits of their permit for effluent discharge.
Management decided to pilot test WaterFX 300 to determine its ability to maintain a low TP limit using much less coagulant volume, less caustic, and the potential to decrease the solid waste sent for disposal.
TRIAL OVERVIEW: CHEMICAL P REMOVAL
Starting in November 2121, WaterFX 300 was dosed directly into the aerobic zone prior to the MBR, and the use of alum was suspended at the same time.
During the months of November and December, the plant made minor adjustments as they learned how to balance the WaterFX 300 feed to match the incoming flow and TP of the plant and keep the effluent safely under the effluent limit. This was accomplished quickly as the feed of WaterFX 300 required only a few ml/min adjustment each day or every few days to maintain the TP under the 0.06 mg/L (90-Day Avg) limit consistently, compared to alum that often struggled to maintain this low concentration even at a very high dose.
Parameter (at 0.8 MGD) | Pre-May 2020 | Post-Dec 2021 |
---|---|---|
Aluminum Sulfate (gpd) | 100-120 | 0 |
Caustic 50% (gpd) | 35 average | 0 |
WaterFX 300 (gpd) | 0 | 11-14 |
As Figure 2 (below) shows, control over the effluent TP was achieved quickly, and the feed of caustic was scaled down and/or turned off within a few days, as shown in Figure 3. TP was maintained around 0.06 mg/L and often as low as 0.03 mg/L after switching to WaterFX, compared to multiple occurrences of effluent TP exceeding 0.15mg/L while using alum.
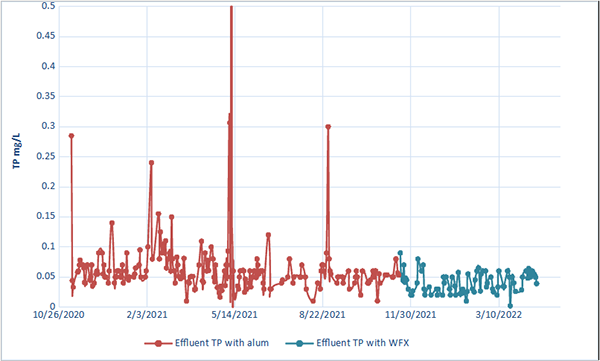
Figure 2: Effluent TP throughout 2021 and 2022 with WaterFX 300 and Alum
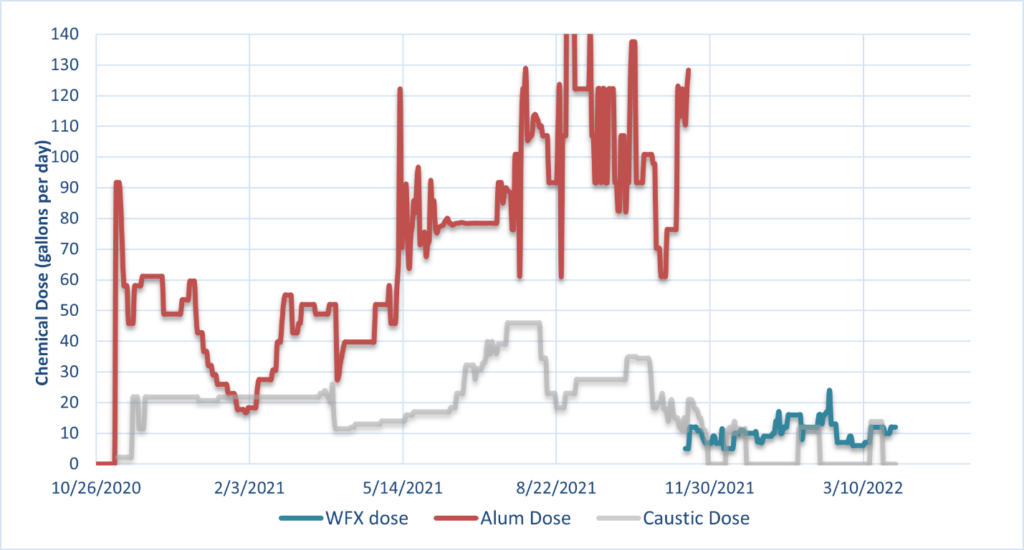
Figure 3: Chemical Usage in 2021 and 2022
Along with demonstrating the ability to keep the TP below the effluent 90-day average TP limit, the switch to WaterFX brought the additional benefits of significantly reducing the volume of chemical consumption. As shown in Figure 3, the average alum dose of 100-120 gallons per day was replaced and TP compliance stabilized and improved using only 11-14 gallons per day of WaterFX.
Alum typically has a pH near 2, making it highly corrosive and acidic. To meet TP limits, facilities often must use such high volumes of alum that severely reduce system pH and consume system alkalinity. Facilities like Jordanelle add extremely harsh and temperature sensitive caustic (typically sodium hydroxide) to the system to neutralize the acidity from the alum, balance the pH and to provide alkalinity for nitrogen removal. While using alum, the Jordanelle plant added 35 gallons of 50% caustic per day on average to offset 100+ gallons per day of alum. By comparison, WaterFX 300 is has a pH of 3-4, which is around 100 times less acidic. Combined with the 10x reduction in volume needed to meet TP requirements at Jordanelle, WaterFX 300 presents an option that introduces around 1000 times less acid to the water treatment system. Due to this reduction in acidic chemical addition, Jordanelle was able to drastically reduce the supplemental caustic, requiring zero caustic most days and only occasional dosing of 10 gallons per day to maintain alkalinity and pH.
Soon after the trial began, 11-14 gallons per day of WaterFX 300 replaced all 120 gallons per day of alum while maintaining 100% compliance, and the average daily dose of 35 gallons of caustic dropped to nearly zero. Focusing on just the cost of these 3 chemicals, the WaterFX solution is expected to save JSSD $24,900 per year.
SLUDGE REDUCTION
A secondary benefit of reducing coagulant chemical volume is sludge production. Chemical coagulants like ferric chloride and aluminum sulfate (and WaterFX 300 to be fair) will generate approximately 0.5 lbs. of dry chemical sludge per solution pound of chemical added. When sludge is dewatered to 20% solids (which is difficult, especially with alum or ferric coagulants that bind water) this 0.5 lbs. of dry sludge equals 2.5 lbs. of wet chemical sludge per pound of chemical used. A facility like JSSD, using 120 gallons per day of alum could be making around 3000 lbs. per day of additional wet sludge just from the addition of the alum. Thus, they pay for the alum twice, once to purchase it and again to dispose of the waste it generates. One way WaterFX 300 reduces this sludge simply by requiring less chemical to accomplish the same result, in this case 10 times less chemical, producing less chemical sludge.
Along with WaterFX 300 generating less chemical sludge, JSSD found switching to WaterFX 300 from alum improved their dewatering process. While using alum at 120 gallons per day in the weeks before the trial, the belt press typically produced a cake around 16.5% solids by weight. After switching to WaterFX 300, the belt press produced a dryer cake, at around 17.5%. This improvement from 16.5% to 17.5% represents a decrease of 6% of total wet solids for the same quantity of dry solids.
The combination of generating less chemical sludge and dewatering to a higher percent solids from the belt press directly resulted in fewer tons of biosolids sent to disposal. While using alum throughout 2021, the facility wasted approximately 5.1 tons of wet sludge per million gallons of flow. After switching to WaterFX 300, JSSD wasted approximately 4.4 tons of wet sludge per million gallons of flow. This represents a total sludge reduction of almost 14%, saving on disposal costs.
Highlights while using WaterFX 300
- TP was kept in total compliance with 11-14 gpd of WaterFX 300 vs 120 gpd of alum, which failed to consistently achieve compliance even at high doses.
- The need for caustic addition was nearly eliminated.
- Belt press cake solids increased from about 16.5% to 17.5%
- Total sludge was reduced by about 14% when accounting for flow increases.
ADDITIONAL BENEFITS OBSERVED
The JSSD facility receives remote monitoring reports from Suez the manufacturer of the MBR membranes used at the facility. The reports showcase membrane flux (flow per membrane area), turbidity, transmembrane pressure (TMP), and permeability. The reports showed no noticeable change in any of these characteristics during the chemical transition and throughout the year of using WaterFX. This demonstrates that in this MBR application, WaterFX does not foul or interfere with the membranes in any way that impacts performance even when used with colder flows in winter.
RESULTS and CONCLUSION
There were many operational and monetary benefits from this trial at Jordanelle SSD:
- The TP concentrations were maintained at or below the low permit limit of 0.06 mg/L throughout the trial period while using WaterFX 300, compliance that even extreme doses of alum could not achieve.
- The financial savings of changing to WaterFX 300 from the previous combination of alum coagulant and caustic saved the plant an approximately $24,900/year.
- The belt press cake % solids increased after changing to WaterFX.
- WaterFX 300 reduced the volume and weight of sludge from the facility – disposal weight decreased from 5.1 to 4.4 wet tons per million gallons of flow, saving on disposal costs.
During the entire trial period there were no reported instances of non-compliance and since that time the plant has been in total compliance with its National Pollutant Discharge Elimination System (NPDES) discharge permit while continuing to use WaterFX 300.
The JSSD WRF facility is convinced that the WaterFX 300 trial was a success and is continuing to use the WaterFX 300 as their coagulant.